12/31/04
I finally have a chance to
post an update detailing the experiences I had during the repair of the Jeep following the crash. This update took far too long.
The root cause was located in the fact that the body shop I used managed to drag out the
repair for an incredible six weeks; two weeks past the estimated due date. In that
time the events that transpired tested my patience to the limit. The time limit on
the rental car ran out, I was called twice and told that the Jeep was "done" and
I could pick it up, and on more than one visit in between, I found conditions that defied
explanation.
I need to qualify my story
that follows by saying a few things about my past experience with crashes, body work, and
automotive work in general. First, I have had more than my fair share of crashes.
In most cases it has not been my fault, in the technical sense, though I admit I
may have had a part in some of them. Between the times that I have had my car in a
body shop for repair, I have also restored a number of cars myself. Not just little
touch-up spritzes with a can of matching paint - full-blown frame-up restorations with
engines, tranny's, dashes, wiring harnesses. In short, I have had more than one car
completely stripped down in my garage. I have rebuilt engines, carburetors, and just
about everything in between.
My personal, hands-on
experience was brought about as a result of three main issues:
I had over the years
migrated away from using shops because I couldn't afford it, didn't like the way most
mechanics did the work, and often found myself needed repairs at times when a shop was not
available. I bought a complete array of tools including such things as clutch
alignment tools, engine hoists, a compressor and many attachments, and so on. In
recent times, after a couple of long projects restoring cars and owning more contemporary
cars, I had surrendered to the Volvo dealer for repairs to my wife's car, and stayed with
fixing the Jeep myself as much as possible.
So in summary, I have been
there, done that, got the T-Shirt when it comes to having my vehicle repaired by a body
shop, and have also done quite extensive work of this type myself. So when I tell
the story about having the Jeep fixed after the crash, it is not a paranoid rant from an
ignorant fool. It is an objective account of what really happened and how terribly
wrong things can go. Ignorance on my part might have been bliss but it would not
have fostered success.
Part One
I got lucky one day and
stopped by when the Jeep was on the frame machine. I got some pictures of it all set
up for the pull.
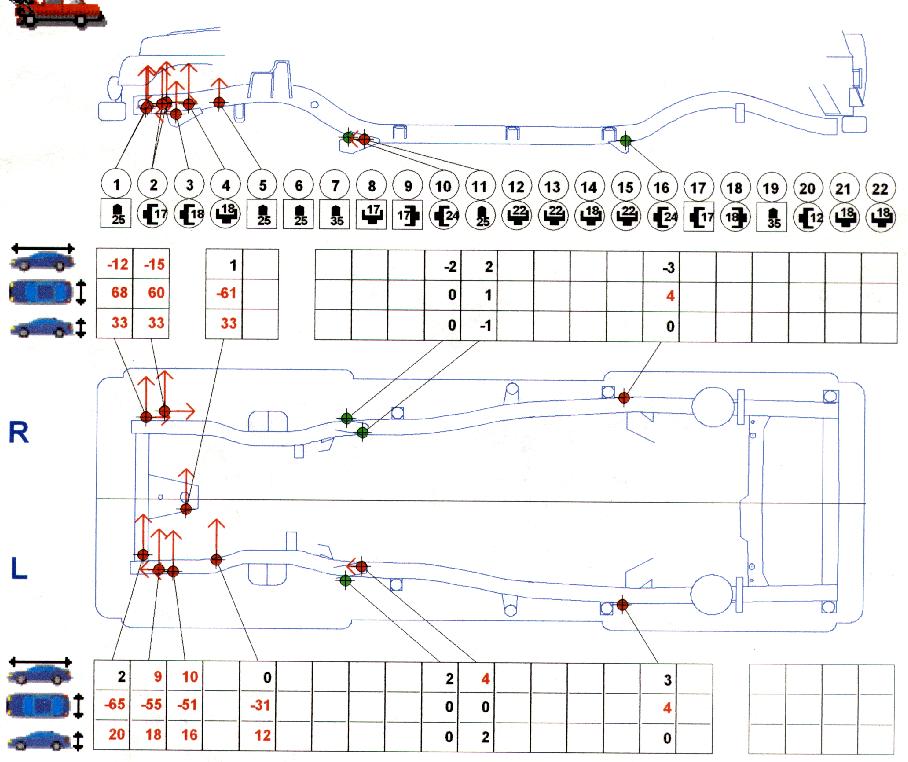
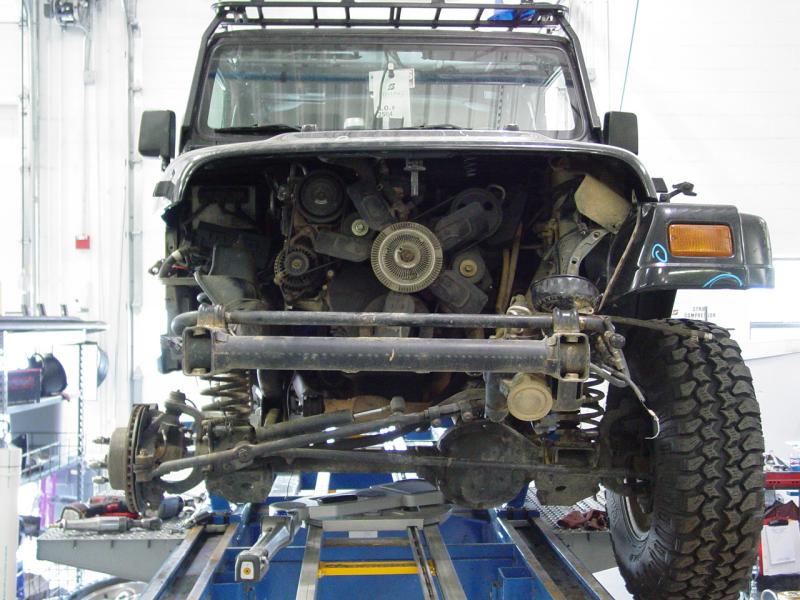













And again after the frame
was straightened:
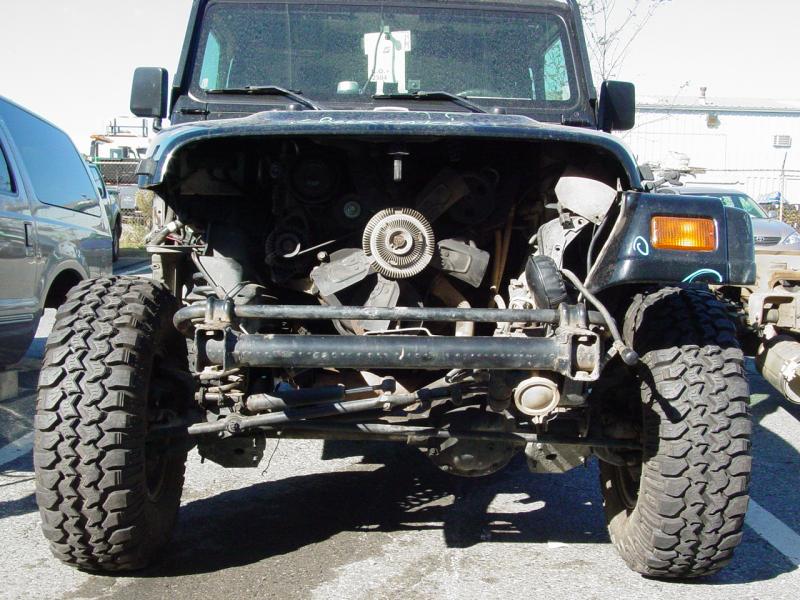



The story is already quite
long so I am trying to keep it as short as possible. Let's just say I got a call
telling me the Jeep would be ready to be picked up on November 20. I showed up later
in the morning to find that the Jeep was way out in a corner of the shop and a few guys
were trying to figure out how to put something back together. It was almost comic
except that it was MY Jeep and they seemed pretty clueless. To say it was far from
being "done" would be an understatement. It was not assembled. The
freshly painted fender had been damaged while drying and was in need of repainting.
The flares were not installed and the wiring to the side markers on one flare had been
very creatively (and incorrectly) rerouted.
But the kicker was the
winch. It was installed backwards! What the...?! Sure enough, it had been
installed facing the rear of the vehicle. This posed no significant challenges as
anyone who has ever installed a winch knows, it can be corrected by simply removing it and
turning it around. So I laughed at it (the "technician" didn't see the
humor) and pointed out that it needed to face the other way. During the short
conversation that followed when the technician attempted to tell me that the winch was
indeed installed correctly I found that the powdercoat finish of the winch was heavily
gouged down to bare metal. It looked like it had been dragged on the ground behind a
speeding vehicle! It is still hard for me to imagine what could have happened to
cause this damage. I contained my outrage and called it to the attention of the shop
manager. He tried to claim it was due to the accident and that the winch was going
to stay that way. I took him to this page and showed him the picture of the winch
AFTER the accident but BEFORE the Jeep was brought in for repair. With his mouth
hanging slack he agreed that in fact the winch had not been damaged by the accident.
A word to the wise here: Take pictures of your vehicle often and do not
assume that your vehicle will not be further damaged between the time you crash and the
time it leaves the body shop. That picture of the winch after the accident got me my
winch replaced because of the gouges that the shop caused.
Here is the list of
incomplete tasks following that visit to pick up the Jeep (remember, they called me to
tell me to come and get it):
Issue |
Parts |
Comments |
Winch has
significant damage not present when vehicle left for repair - Major scratches on face of
winch |
Winch |
review pictures showing winch AFTER crash, before left for repair and it is clear
that no damage to winch exists. http://4x4icon.com/offroad/1015_crash/dsc07269.htm |
Winch Installed Backwards |
Winch Plate, tow hooks |
rear hold-down bolts (sway bar) not installed, require proper
spacers below winch plate and above sway bar hold-down |
battery spacer not installed |
battery spacer |
red rectangle interlocks under battery bottom to give battery
proper height for battery hold-down bracket and bolts |
cracked cover still cracked |
relay box end cap |
see photo here |
air chuck not mounted to bracket left side front bumper |
screw missing |
|
steering box skid plate lower retaining nut and bolt not installed |
requires Grade 8 hardware |
loose nut still inside box member adjacent to steering box but
should be replaced |
incorrect marker light socket and lens on passenger side fender (metal portion of
fender facing front) |
marker light socket and lens |
note drivers side socket and lens - different reflector pattern,
different colored socket. Passenger front |
headlight grills not installed |
springs held by headlamp door screws; headlamp grills held by
brackets and springs (brackets missing, 3 per side) |
|
All harness and A/C retainers missing from vehicle |
|
|
grill center support bolt not tightened/centered |
|
|
fan binding on fan shroud |
|
|
external temperature sensor not installed on bumper |
|
|
winch plate not bolted with sway bar bolts |
|
requires spacer washers between winch plate and sway bar
u-brackets to span space between, may require longer bolt; must use Grade 8 hardware |
grill/radiator supports (rods to firewall) not straightened. painted or installed |
|
|
radiator hoses not installed |
|
|
hood safety latch still heavily damaged, not working correctly, unsafe |
replace part! |
|
hood hold-down latches (left and right) not properly aligned, not holding hood
down |
|
need to align bracket and base so rubber makes straight line
between them, and latch closes over-center and will not release accidentally |
radiator splash apron not installed |
|
under radiator near front of vehicle |
wheel lug nut broken - was not broken when vehicle left for repair - see photos |
|
|
hood - lower edge inside passenger side has paint removed from post-sanding touch
up - bar metal showing |
|
needs to be painted properly to prevent corrosion and flaking |
|
|
|
RETURN ALL PARTS LARGE AND SMALL |
|
|
It should be mentioned that
I had taken a day off from work, driven what ended up being 400 miles round trip, and
canceled the rental car in order to pick up the Jeep. The inconvenience caused by
their inability to properly assess the status of the Jeep was significant. My anger
was kept below the surface - just...
Part II
So I spent the next week
away from home driving the rental and hating every minute of it. I was unable to go
wheeling, did not have the use of my stereo (wah!) and had to live with my GPS being
plugged into the cigarette lighter instead of mounted on a bracket and hard-wired
(double-wah!). By the time Friday rolled around, I was going nuts. I got
called again to come get the Jeep and I ran through the list above to be sure that
EVERYTHING really was done. I was assured everything was done. I would soon
find out it was not.
I arrived to find the Jeep
still being worked on but was told it would be ready in a few hours and to come back then.
I took a deep breath and left for two hours then returned. The Jeep was
parked outside in the area used for customer cars ready for pick up. I went over it
and found most of the items on the list above had been corrected. But there were
still a littany of issues.
In the pile of old parts I
discovered many parts that were not replaced and not installed on the Jeep. The two
most significant were the VIN plate from the front grill and the vacuum reservoir for the
heating/cooling system.
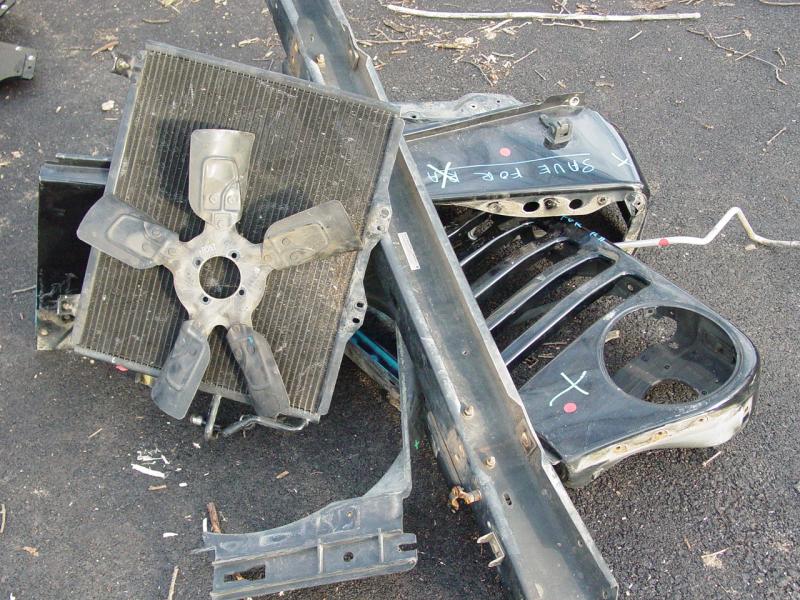

I also found parts missing
that were present when the Jeep was left for repair. Some left over new parts that I
purchased separately were also missing.
I took all the parts and put
them in the Jeep. I registered my objections with the woman who works the counter.
She was the one shining light in the whole experience. She was always on time
with the correct work products for me. Such a shame that the shop she stood in front
of was so bad. I was to tell her several times how happy I was with her service
right behind bitching out the manager for the incompetence of the technicians...
I took the parts home and
set about installing the vacuum reservoir. Had the tech done it during the repair,
with would have been a simple matter to unscrew it from the old fender and screw it onto
the new fender. But now because it is located inside the mounting bracket on the
cowl, it was necessary to remove the battery and battery tray before installing it.
On the way home from the shop I had turned on the heat and the lack of this part had
caused the flaps inside the dash to slam open and break. So I was not happy.
During the drive home I also
discovered that the Jeep was shaking so bad it would not be driveable. I called the
shop before I even got a mile away to report my findings (heating damage and vibrations)
so that it could not be claimed later that I did these things myself later. I can
not emphasize enough how critical this would become the following Monday when I returned
to the shop.
Once home, I got under the
Jeep and found a large and very fresh dent in the front driveshaft. It was shaped
like the part of a floor jack that the vehicle rests on when jacking... I
disconnected the driveshaft from the front axle to eliminate the vibration temporarily so
that I could drive it until it could be fixed. My "not happy" went to
burning rage. How could this shop make so many major mistakes and stay in business?
I did some breathing exercises, ate some food, and resolved that it could all be
fixed and I would not be paying so it was but a temporary glitch. That dulled the
anger that I had and allowed me to get through the weekend without killing anybody.
I sent the shop manager an email message to further document the problem:
"I have had an opportunity to take
the vehicle out for a drive and find that there is a strong vibration in the drive train
that was not present before the accident. It is much worse than I first thought. The
vehicle is nearly undriveable at speeds above 40 MPH. It vibrates very badly. I suspect
that something in the front axle, front drive shaft or transfer case is not right. This
will need attention right away. I am in a particularly bad position because of course now
I have returned the rental car. Also, I had a very full weekend planned and must travel to
work and back early next week (200 miles each way).
I am registering this problem with you
so that I can get it fixed with you, but I am very concerned about the schedule. I cannot
leave it for another six weeks. I need pretty instant results. And I am concerned that you
will not be able to diagnose and correct the problem because you don't specialize in 4WD
vehicles. Please tell me what we can do to get this right?
<Manager's name>, it will be
problematic enough if the vehicle is not repaired by Wednesday, December 1, but if it goes
past December 6th, I will no longer be living in Gaithersburg! I will be permanently
located 200 miles away in Morgantown. My work schedule is so full I will be unable to
travel back and forth to Gaithersburg on weekdays, and even Saturdays could be a problem.
So please, with this schedule in mind, I
need rapid resolution, but of course I want the work done correctly. I am thinking it
would be worthwhile having the front drive shaft checked by a specialist (Jeep Dealer),
and replaced if necessary. Please note that it could have been damaged in the crash and be
the source of the vibration. It's a bolt-on repair. But there is also the possibility
that the front axle or transfer case is damaged. I guess we'll have to work through the
problem to a solution and see what turns up. I may start diagnosing it Saturday morning
(the front drive shaft can be disconnected to see if the vibration goes away)."
On Monday I went in to the
shop. The manager who through the whole experience was bright and cheery and very
good about promising to get things right, came to the door to greet me. I must
confess I'd had enough of his inability to manage and invited him outside so I could tear
him a new one without having the pieces litter the front office. I must admit that I
managed to stay on topic, didn't call him any names, but was perhaps a little bit louder
than I should have been. I gave him a list of things that needed to be corrected:
Require attention by <shop
name>:
The A/C system does not appear to be
cooling. Please check and correct as needed
The front Drive Shaft needs to be removed
and replaced.: <dealer name>
Gaithersburg, MD Counter Person -
<name>
VIN (number)
Front Drive Shaft Assembly Part Number 52098 377 AD.
Front U-joint may not be included with
drive shaft assembly please be sure to order it if necessary
There are paint issues which we discussed
when I picked up the vehicle.
Oil Pressure Sending Unit not working
properly (screws into right side of block) need replacement part
Missing Parts Provide to
Customer:
The new fender flare extensions that came
with the new fender flares that I paid for and were on the cart last I came to look at the
Jeep are missing - I paid for them and I need them. They are not inexpensive.
They are the short straight parts that go at the bottom rear edge of the front fenders.
Reimburse for parts not installed:
The radiator overflow hose to reservoir is
punctured and leaking coolant.
The mounting studs that hold the air
filter box to new fender were broken and left on the old fender, Stray hardware
without washers was used to install air box instead of the correct special parts that
raise the part up off the fender and isolate it with rubber bushings.
The Battery insulating material that
protects the battery from overheating was not installed, it was found in parts bin ripped.
The main battery wiring harness anchor clip
was not anchored to the new fender (harness clip broken, left dangling in space)
various broken clips holding wire harness
and brake lines need to be replaced.
Resolved by Customer:
A vacuum box on lower rear of right-front
fender was left on the old fender; and was not installed on new fender.
The vacuum hose was left dangling in space.
The VIN ID Plate for the front cross member
was left affixed to the discarded grill part, it should be installed on the new grill
The interior heater/cooling vents are not
working after loud "POP!" within minutes of starting vehicle. (vacuum box
install corrected HVAC problem)
The winch plate center bolt not bolted to
frame, was left dangling loose.
The brake lines left unanchored running
across the front of vehicle with anchor clips broken.
The Left front turn signal on fender flare
is "flaky" - sometimes it works, sometimes it is off.
For some inexplicable reason, the drain
tubing that allows condensation to drain from the a/c was modified. The factory hose
coming out of the firewall is missing and the extension tubing that I installed to
lengthen the factory tube has been put in its place."
Wow. That's quite a list for a vehicle
that has twice been statused as "done"...
I brought the Jeep back to have the drive
shaft installed only because we were moving to a new home and I was scheduled to be with
the movers all day and could not do it myself. I had no choice really. The
list above clear states that I fixed the vacuum reservoir problem but for some reason I
can't understand, the "technician" attempted to take it apart anyway, then tried
to lie to me about the work he did. At this point it was all too much. I
nearly got in a fist fight with this mouth-breathing sack of b.s. I chose instead to
walk away.









In the course of six weeks I was lied to,
had my vehicle fixed with aftermarket parts that were not authorized, twice called to come
pick up a vehicle that was clearly not ready to be driven, and had several other things
damaged that were not related to the crash. I ended up doing a lot of work myself,
diagnosing several of their mistakes and generally being my own advocate. In the end
I wished that I had never let them lay hands on my vehicle. But the best was yet to
come.
A week after I got the Jeep back, I was
driving back from our new home (200 miles away) and the engine blew... Remember that
line item for the oil pressure gauge? The oil pressure gauge was fine - the engine
really did have low pressure and ultimately self-destructed on a deserted highway one hour
before I was to arrive for the settlement meeting to sell my old home... Bob the
Builder Can You Fix it!? Bob the Builder Yes We Can!
The engine failure was unfortunately too far
apart from the crash and subsequent body shop debacle to be considered part of the
accident so that bill came out of my ass. See
the story describing that fun!