My friend
Dave and I talked at length about my Jeep. He eventually
decided he'd like to have one as a second vehicle. He located a
nice TJ and showed up at work one day all smiles. Not long after
that, he started going over different accessories and modifications that
he was considering. I think it's safe to say that Dave has the
Jeep disease. I am not sure if he caught it from me, or if it lie
dormant for years. But regardless of the source, I felt it my duty
to help him embrace it.
Along the
way, the topic of shocks came up. I don't remember the exact
conversation, but Dave indicated that he wanted to improve the ride of
the Jeep and had found the Rancho Shock system. He wanted to know
what I thought. I don't usually have any problem giving my opinion
but had to admit, at least to myself, that I didn't know very much about
Rancho's shocks. What I did know was useless. That is to say, I
harbored a 30-year old impression of rusty old Ford and Chevy pick-up
trucks with noisy, jacked up leaf springs. Plastered all over the
shocks and often the rest of the vehicles, was the Rancho name.
Let's just say that comparing my brand recognition experience with other
brands, like Bilstein or KYB, it left me thinking that Rancho was not a very
distinguished trademark. But I try to be fair. So I dug back
into the research I had been doing about suspension systems.
My friend
Roscoe and a couple people installed Rancho lift
kits. The prevailing opinion of those folks was that the lift kits
were well designed, offered great value for the money, and came with
everything needed to install a well-engineered suspension system.
The resulting performance is also very good. So I updated my view of Rancho to allow for the possibility that my recollection
of their products was out of date and ignorant. I took another
look at their shock absorber systems. I found that the products
are in widespread use, appear to be well regarded, and while somewhat
expensive, appear to perform as represented.
|
So with
all this churning, I felt that Dave was probably looking in the right
direction with his desire to improve the shocks on his TJ. I don't
think I specifically recommended a solution. He came in my office
a few days later to tell me that he had purchased the Rancho® Dual-action Remote Control System, Part No. RS9700
that includes the 5-position shocks, the remote control system that
consists of a small air compressor, air lines, and a head unit.
Wow. The concept looked pretty cool. It sounds like a long
way to go for a cup of coffee, but anyone who has climbed under a muddy
4x4 will tell you, fumbling around to adjust a knob on four shocks is
probably not high on anyone's list of things to do. So if you want
to have adjustable shocks, the remote control sure sounds like the way to go. |
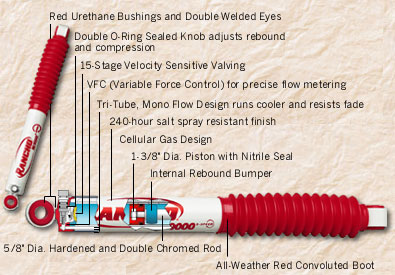 |
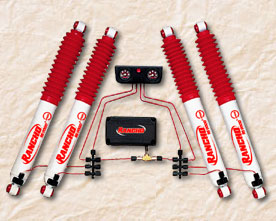 |
I agreed
to help Dave install this wondrous collection of devices. I was
very curious about it, and thought it would be a great way to get up
close and personal with it since I too am considering shock
options. It was a few weeks before our schedules coincided but
finally the day came when we could set about putting it together.
I felt confident about removing and replacing the shocks as I have done
it once on the TJ and countless times on other vehicles. I was
less confident about the remote control system but reasoned it would not
be any different than installing a high-end stereo system, or perhaps
running a complete set of brake lines, both jobs that I have done on
numerous occasions. |
Remote
Control Location and Installation |
|
There
were some problems that had to be worked out before we could really get
started. The TJ has limited places where the remote control panel
can be installed. Some people have chosen to cut holes in their
console or dash and install the gauges and switches that way. We
looked at some of these options but concluded that it was not a great
solution for Dave. In the end, Dave decided that he'd like the
remote control unit up on the coin tray where he could touch and see it
easily. I am inclined to agree even though that created some new
problems. Mainly the issue is that the bracket supplied is
intended for under-dash applications. As such, the lines running
to the remote are exposed, looking a little like the back of a really
small stereo. We also had to use a couple of grommets to raise the
bracket so the buttons and inputs would clear the recess of the coin
tray. |
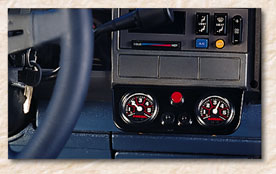 |
|
Once these
issues were worked out, I removed the fascia panel surrounding the
radio, heater and ash tray. This involved the removal of a vent
cover on the dash - just snapped it out carefully, and the removal of
three screws that held the fascia in place. It is a little tricky
to pry it forward around the radio, etc., but it came right out. I
measured the location of the mounting holes and drilled them out,
centering the bracket front and rear, and side to side. This
leaves enough room to get the inputs hooked up in the back and enough
room in front to operate the controls. |
I
assembled the remote control components onto the bracket. There
are two pressure gauges, one power button for the compressor, and two
pressure-release buttons, one for front and rear. This assembly
was straightforward. The pressure-release buttons are a bit quirky
and required some thinking to prevent marking them up. |
|
Compressor
Location and Installation |
|
|
Next,
following the instructions, I separated the cover and base of the
compressor unit to gain access to the mounting holes in the base.
Dave's installation was facilitated by the lack of ABS and attending
systems. The platform where ABS is usually located was vacant
except for the remains of a fastener that was used to mount a now
absent security system. I removed the rusty old fastener and we
evaluated which way to install the compressor. We ended up with
the brass "T" fitting closest to the firewall and the power
wires coming out the front of the compressor box. We marked and
drilled the holes, then mounted the box to the vehicle using the
provided sheet metal screws. The wiring harness for the power
going to the compressor was provide and proved to be very well
done. We added a spade connector to the existing spare
"Switched" power connection behind the glove box, and tied in
the Rancho compressor. I used one of the mounting screws for
ground wire right where it was screwed to the mounting surface. We
ran the connection to the switch on the control panel and testing
revealed that the compressor worked. |
Shock
Conversion and Installation |
|
Since the
installation instructions are oriented to the conversion of existing
Ranch Shocks, it lays out the order of steps assuming the shocks are
already installed. Instead of installing the shocks first, I
installed the fittings onto the shocks on the bench - why contort myself
if I don't have to! The conversion involves the removal of the
rotating control knob and the installation of the air fitting and
"O" ring. This was pretty easy to do on the new shocks
that Dave bought. The control knobs come off easily and the air
fitting and "O" ring just take their place. Once the air
fittings were installed, I installed the shocks. I suppose there
are folks who think it is easier to do with wheels removed. But we
just drove the Jeep up on ramps and swapped out the shocks. There
are no special considerations except to say that the fasteners from the
old shocks are reused. The new shocks come with bar pins inserted
for the rear shocks and a new nut for the top shaft on the front
shock. They also are supplied with new bushings already installed
on the rear, and ready to install on the top front. |
|
|
Time to
install the shocks. We debated mounting the air connections at the
top where they would be protected. In the end the decision was
made for us in the front because the shocks will only mount one
way. It was no big deal up there because the air connection is
sufficiently protected from knocks by the way the shocks are
mounted. In the rear, we oriented the air connections to point
toward the front of the vehicle. This places them inside the lower
shock mounting bracket, again, well protected from most types of damage. |
Air
Line Manifold Location and Installation |
|
We had to
decide where to locate the two manifolds that distribute the air
connections from the compressor. We considered mounting them under
the Jeep on the frame rails. We looked at various places in the
engine compartment. In the end, we decided to mount it on the
bracket that is adjacent to the ABS shelf, near the shock system compressor. I drilled a new hole and we bolted the two manifolds
side-by-side. This places it away from engine heat (well high heat
anyway), up where it is accessible for maintenance, and out of the
elements. I think it turned out to be a good place for it since it
made assembly quite easy. This location will not work for Jeeps
with ABS or other components installed on the ABS shelf. |
|
Air
Line Locations and Installation |
|
|
The air
lines need to be routed from the distribution manifolds to the
shocks. There is one line for each shock. The purpose of the
line is to activate the valve formerly controlled by the rotating knob
that is removed when the remote control is installed. The entire
system has to be air-tight. The air lines are connected to the
shocks and travel along the axle and frame to the manifold and
compressor. This means that the air lines must transition from the
frame (non-moving) to the axles (moves with movement in the suspension) |
I decided
not to hurt my head figuring out how to solve the problem of mounting
the air lines to the shocks in such a way that the lines would be
protected and move without limitation. My source of inspiration
was my own Jeep: It has ABS and each wheel has an ABS
sensor. This wiring has exactly the same considerations and nearly
the same mounting points throughout. It was a very easy matter of
reviewing my ABS layout and then routing the air lines the same way on
Dave's Jeep. |
|
|
Basically
the air lines descend down from the air compressor to the frame rail
below the driver's feet. From there, the front lines follow the
left lower control arm. The left line connects to the left
shock. The right line is wire-tied over the top of the axle to the
other shock. I used some wire loom wrap to protect the air line in
places where movement was possible. The rear lines follow the
brake lines all the way back to the rear axle where the left and right
lines branch off to their respective shocks. |
Each air
connection requires a different length of air line. We
"fished" the line back to the shock in question from the front
of the Jeep, making sure not to tangle the air line in any other wires
or lines. I wanted to make sure that any other systems were left
separate from this one so that servicing will not be complicated by
tangles. This required fairly constant watching to make sure that
we kept ourselves honest. This was especially true working around
the steering column since it would not do to have the air line get
wrapped in the column. |
|
|
We fished
each line down to a shock, left a little bit of slack and made sure that
each change of direction had plenty of curve to prevent kinks. I
cut each air line connection square, starting the job with a new
razor knife blade. I put a connector onto the air line, added the
itsy-bitsy "O" ring, then connected the air line to the
fitting, making it finger tight. I made sure to seat the air line
in the connection, and avoiding cross threading and
over-tightening. Naturally I made sure that no dirt got into the
system. |
We worked
our way through this slowly, taking our time to check and recheck the
routing of the lines. When we were satisfied that the lines were
properly connected, we organized the air lines and wire-wrapped them to
the main wiring harness on the fire wall, routing it away from the
exhaust manifold and steering column. Two openings on each of the
manifolds are to be closed off - they are for use in dual-shock
applications. I put the plugs for these in and screwed on the
connectors. |
|
|
We left
the gauge lighting wires unconnected. Dave will connect them to
something that receives power when the other dash lights receive power -
probably another dash light power source can be borrowed to power these
lights. |
Testing
and Troubleshooting |
|
Once
all the lines were run, all the components were in place, and the shocks
were converted and installed, we were ready for our first test.
This came after a leisurely afternoon of slow working, talking, more
working, and breaks for food and drink. We hoped it would work
with our first try. We hoped there would be no air leaks or
component failure. Dave started the Jeep and pushed the control
for the compressor. The needles swung into action and climbed
towards the "5" on the dial. When they reached it, he
let off the button. Immediately, the gauge for the rear started
going back down to zero. The gauge for the front slowly did the
same. We had a leak somewhere... Darn! it was already
dark and we were both tired. Neither one of us was interested in a
long protracted diagnostic session. So we took a sanity break and
let it sit for a minute. We took a drive to see if we could feel
the difference in the shocks, playing with the controls to see if
anything improved. It did not. |
|
|
After we
cleaned up the accumulation of rubbish that had collected while we
worked, we decided to check the connections for leaks. We
erroneously concluded that there must be a problem with the rear side
since that was the side that had leaked down fastest. That reduced
the number of fittings to check. I mixed up some clean soapy water
and dribbled it on the manifold connections while Dave ran the
compressor. Immediately the problem became obvious. The four
plugged connections were spewing bubbles like a child's toy! I had
not installed the "o" rings on these connections because I
didn't think they were needed. DOH! I could not have been
more wrong. I put the O-rings on and we repeated the test.
This time, the pressure did not leak down. When Dave pushed the
button for the compressor, the gauges went up to "5" and
stayed there without moving. We took it for another ride on the
road and this time we were treated to the full operation of the system. |
We set
the shocks to various settings from "1" (Soft) to
"5" (Hard). The system works like a champ. Dave
can match the shocks front and rear or run either the front or rear
softer or harder than the other. The separate adjustments are
somewhat strange because pressurizing the system loads up all the shocks
to their maximum pressure setting. So you have to bleed down the
end that you want to run softer after pressurizing all four
shocks. It's not really too bad, just takes some getting used to. |
|